- Title
-
6 häufige Fehler in der Supply Chain Strategie vermeiden
- Section
- Insight
- Summary
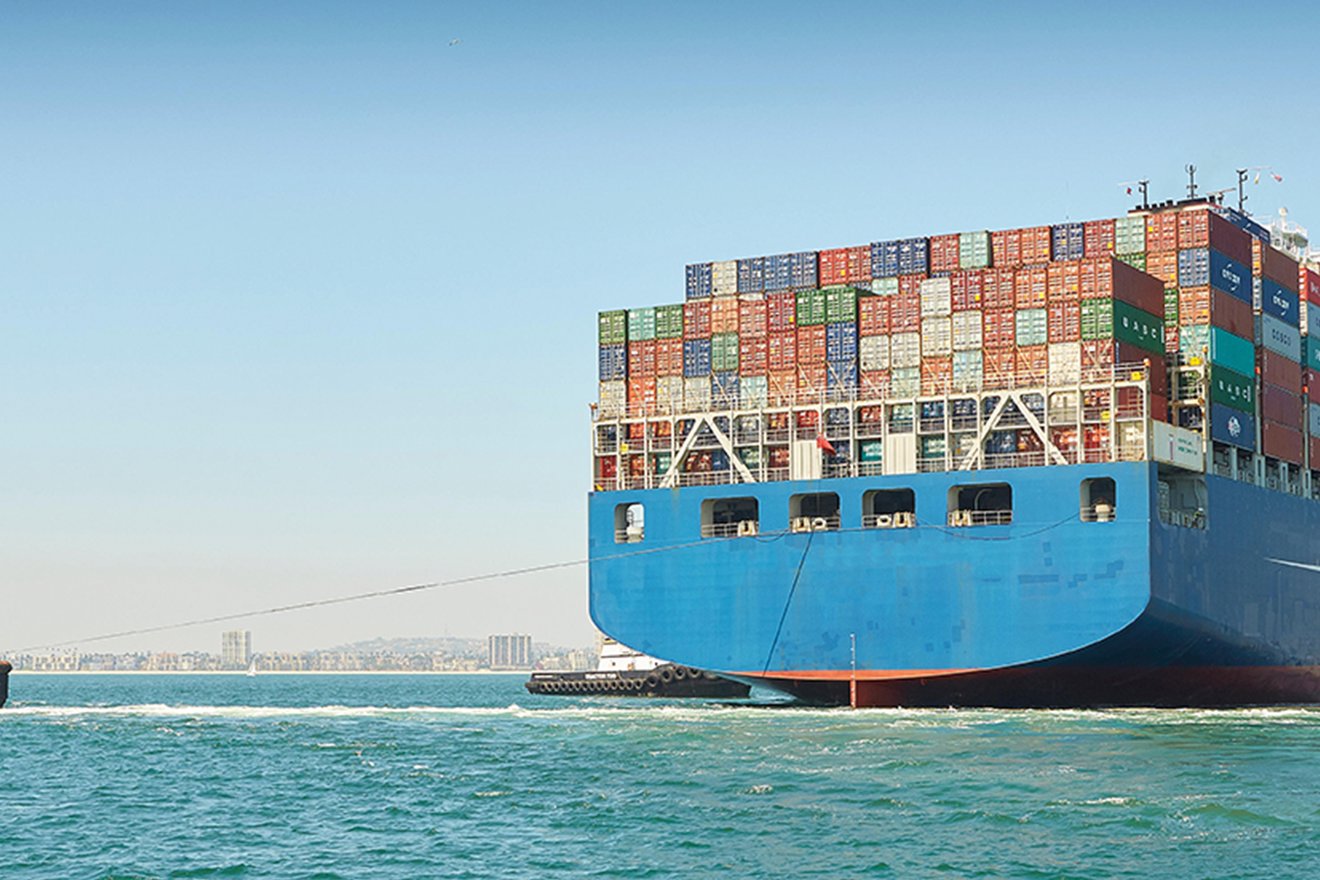
Die meisten Unternehmen entwickeln ihre Supply Chain Strategie stückweise im Laufe der Zeit. Das kann dazu führen, dass sie irgendwann nicht mehr zweckmäßig ist. Wir zeigen einige typische Versäumnisse auf.
Jede Führungskraft im Supply-Chain-Umfeld weiß um die Bedeutung einer effizienten und gut gemanagten Lieferkette. Produkte müssen in den korrekten Stückzahlen, zum richtigen Zeitpunkt und so kosteneffizient wie möglich geliefert werden. Die Strategie dahinter sollte sich dabei an den Bedürfnissen des Unternehmens und seiner Kunden orientieren. Außerdem sollte sie Risiken minimieren und sicherstellen, dass die Organisation ethisch verantwortlich und nachhaltig arbeitet.
Den meisten Führungskräften ist vollkommen klar, dass eine umfassende Supply Chain Strategie erforderlich ist, die alles beinhaltet – von der Planung über die Lagerhaltung und Lieferung an Filialen oder Kunden bis hin zur Abwicklung von Retouren. Dennoch betreiben viele Unternehmen nach wie vor ineffiziente Supply Chains.
Es gibt eine ganze Reihe typischer Fallstricke im Zusammenhang mit der Supply Chain Strategie. Die gute Nachricht ist allerdings, dass Unternehmen praktisch sofort von erheblichen Verbesserungen ihrer betrieblichen Abläufe profitieren können, wenn sie diese Probleme aktiv angehen. Sie sind dann in der Lage, vorausschauend zu planen, Risiken einzudämmen und die Kundenzufriedenheit trotz niedrigerer Kosten deutlich zu steigern.
Unternehmen können praktisch sofort von erheblichen Verbesserungen ihrer betrieblichen Abläufe profitieren, wenn sie diese Probleme aktiv angehen. Sie sind dann in der Lage, vorausschauend zu planen, Risiken einzudämmen und die Kundenzufriedenheit trotz niedrigerer Kosten deutlich zu steigern.
Fallstrick 1: Keine Supply Chain Strategie haben
Eines der Hauptprobleme, die ein Unternehmen angehen sollte, ist eine unzureichende oder gar überhaupt nicht vorhandene Supply Chain Strategie. Dies kommt häufig bei Firmen vor, die relativ klein angefangen haben und bei denen das Management der Supply Chain Schritt für Schritt aufgebaut wurde. Oftmals wurde die Strategie im Laufe der Zeit dann so entwickelt, dass sie auf die damaligen Bedürfnisse des Unternehmens abgestimmt war. So lag der Fokus möglicherweise auf einem bestimmten Bereich wie Logistik, Lagerhaltung oder Planung. Niemand hat seitdem aber versucht, die Supply Chain zu rationalisieren oder eine offizielle Supply Chain Strategie zu erstellen.
Im Ergebnis kann dies zu einer Supply Chain führen, die Leistungen hervorbringt, die von den Kunden gar nicht wertgeschätzt werden. Oder aber es wird versucht, Probleme zu lösen, die eigentlich gar nicht existieren. Der Großteil der bestehenden Strategien basiert in der Regel auf dem, was das Unternehmen vor einem Jahrzehnt benötigte – und nicht auf heutigen oder zukünftigen Anforderungen.
Eine Supply Chain Strategie ist die übergreifende Richtlinie, die alles zusammenführt und es einem Unternehmen so ermöglicht, den größtmöglichen Mehrwert aus seiner Supply Chain zu ziehen. Sie ist daher absolut entscheidend. Ein Anfang kann sein, eine Reihe von generellen Regeln für die Steuerung der Supply Chain aufzustellen und für eine regelmäßige Dokumentation und Überprüfung dieser Richtlinien zu sorgen. Schon allein dadurch wird eine solide Basis für zukünftigen Erfolg geschaffen.
Fallstrick 2: Kein passendes Organisationsmodell haben
Ein schlecht durchdachtes Organisationsmodell ist ein weiterer großer Fallstrick. In vielen Unternehmen kursieren uneinheitliche Modelle, die sich im Laufe der Zeit als Reaktion auf individuelle Situationen entwickelt haben und nicht miteinander verbunden
sind. Sofern innerhalb der Organisation nicht gerade der dringliche Wunsch danach besteht, nehmen sich Unternehmen nur selten die Zeit für eine ganzheitliche Prüfung, ob ihre Supply Chain nach wie vor den gestellten Herausforderungen und übergeordneten Unternehmenszielen gerecht wird.
Den Ausgangspunkt bildet ein Rundum- Check der bestehenden Organisationsmodelle. Dabei sollten Aspekte wie Strategie, Prozesse und Richtlinien, Performance Management, Technologie und Daten, Mitarbeiter, Nachhaltigkeit und Kosten beleuchtet werden. Dies kann auf globaler Ebene und für die einzelnen Komponenten der Supply Chain erfolgen, also für Bereiche wie Planung, Warenbestand, Logistik und Distribution sowie Lagerhaltung.
Auf diese Weise wird sichergestellt, dass die Strategie, die Prozesse und Richtlinien sowie die Performance-Management- Systeme, die die gesamte weltweite Supply Chain regeln, auch auf lokaler Ebene umgesetzt werden – unterstützt durch die passende Technologie und Mitarbeiter mit den richtigen Fähigkeiten. Auch das Thema Nachhaltigkeit sollte hier mit einbezogen werden. Letztendlich geht es darum, dass alle Teile der Supply Chain auf die übergeordneten Unternehmensziele ausgerichtet sind und kostengünstig agieren.
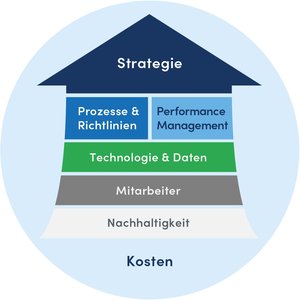
Fallstrick 3: KPIs nicht aufeinander abstimmen
Ganz unabhängig von der Branche haben viele Unternehmen das Thema Kennzahlen bzw. Key Performance Indicator (KPIs) in Bezug auf die Supply Chain Strategie ziemlich ausgereizt – oft so weit, dass dabei von „key“ gar nicht mehr ernsthaft die Rede sein kann.
Einige der erhobenen KPIs sind rein reaktiv, wurden häufig für eine ganz bestimmte Thematik erstellt und sind nur selten organisch aufgebaut. Dies kann dazu führen, dass die Performance der Supply Chain in verschiedene Richtungen gesteuert wird, weil Stakeholder und Fachabteilungen jeweils eigene – teils widersprüchliche – Prioritäten haben. Während Optimierungen auf lokaler Ebene durchaus Standard sind, werden Abstimmungsschwierigkeiten auf der globalen Ebene oft weniger thematisiert. Ein Unternehmen optimiert möglicherweise seine eigenen KPIs vor Ort, aber insgesamt sind sie womöglich nicht auf die allgemeinen Geschäftsziele ausgerichtet.
Während Optimierungen auf lokaler Ebene durchaus Standard sind, werden Abstimmungsschwierigkeiten auf der globalen Ebene oft weniger thematisiert. Ein Unternehmen optimiert möglicherweise seine eigenen KPIs vor Ort, aber insgesamt sind sie womöglich nicht auf die allgemeinen Geschäftsziele ausgerichtet.
Ein Beispiel dafür ist ein Logistikteam, das Sendungen zusammenfasst und dadurch reduzierte Logistikkosten und eine bessere Ausnutzung der Transportkapazitäten erreicht. Die Kollegen im Lager wären im Gegenzug jedoch an bestimmten Wochentagen vom Versandvolumen schier überwältigt und würden zusätzliches Personal einstellen, um ihre eigenen KPIs rund um die Bearbeitungszeiten beim Handling der Materialien zu erfüllen.
Sowohl in der Logistik als auch im Lager werden somit die jeweiligen lokalen KPI-Anforderungen in Bezug auf die Ausnutzung der Transportkapazitäten und die Durchlaufzeiten erfüllt. Die Gesamtkosten für die Organisation sind aber nicht optimal.
Die beste Lösung in diesem Szenario wäre, dass das Logistikteam mit dem Lagerteam zusammenarbeitet und einen Lieferplan erstellt. Darin könnte zum Beispiel die gleichmäßigere Verteilung von Sendungen über die ganze Woche enthalten sein. Nebenbei könnte dies dazu beitragen, die Lagerbestände insgesamt zu senken.
Ein Ad-hoc-Ansatz für KPIs führt in der Regel zu einer übermäßigen Menge von Kennzahlen, die nicht vollständig auf die allgemeinen Geschäftsziele ausgerichtet sind. Unternehmen sollten stattdessen eine entsprechend abgestufte KPI-Pyramide einführen, bei der die höchsten KPIs die Management-Kennzahlen sind.
Eine Produktionsstätte zum Beispiel könnte auf höchster Ebene KPIs haben, die auf der Herstellung einer bestimmten Anzahl von Motoren pro Monat oder pro Jahr basieren. Untergeordnete Metriken ermöglichen es dann, tiefer in diese Kennzahlen einzutauchen, eventuell auch auf Abteilungsebene. Dabei kann es sich dann beispielsweise um pünktliche und vollständige Lieferungen in der Logistik handeln oder die 100-prozentige Verfügbarkeit von Maschinen und Ressourcen. Führungskräfte erhalten so einen deutlich besseren Überblick über möglicherweise vorliegende Probleme. Per Drill-Down lassen sich gezielt die Details der KPIs näher betrachten, in denen das Unternehmen möglicherweise unterdurchschnittlich abschneidet.
Zum Einsatz kommen sollte ein Rahmenwerk für das Performance Management, mit dem auf jeder Ebene der Organisation relevante Kennzahlen bestimmt, bewertet und eingeführt werden können. Wichtig ist dabei, dass diese jeweils auch in die Kennzahlen der darüber und der darunter liegenden Ebene eingebunden sind.

Fallstrick 4: Die Belastbarkeit der Supply Chain nicht überprüfen
Ein ebenfalls sehr häufiger Fehler ist es, die Widerstandsfähigkeit der Lieferkette nicht zu überprüfen. Es gibt mehrere interne und externe Faktoren, die sich auf die Funktionsfähigkeit einer Supply Chain Strategie auswirken oder negativ für das Image des Unternehmens sein können.
Ein großer Anlass zur Besorgnis für viele britische und weltweit agierende Unternehmen ist derzeit der Brexit. Firmen müssen sich damit beschäftigen, wie sie die Produktionsanlagen in Betrieb halten oder für weiterhin gefüllte Regale im Einzelhandel sorgen. Zu anderen potenziellen Bedrohungen weltweit zählen Ausfälle bei Lieferanten, Störungen der Transportwege (man denke hier etwa an den Vulkanausbruch in Island) oder steigende Rohstoffkosten. Risiken für das Image des Unternehmens können durch Kinderarbeit, unzureichende Umweltschutz-, Gesundheits- und Sicherheitsvorkehrungen oder gar moderne Sklaverei entstehen, wenn solche Praktiken irgendwo in der erweiterten Supply Chain aufgedeckt werden.
Efficio hat 14 Risikokategorien identifiziert, um die Widerstandsfähigkeit von Unternehmen zu testen. Gleichzeitig können diese Kategorien genutzt werden, um Notfallpläne zu entwickeln, mit denen die potenziellen Gefahren in Schach gehalten werden können.
Fallstrick 5: Die Kosten des Netzwerks außer Acht lassen
Wenn man die Kosten der einzelnen Elemente der Supply Chain nicht versteht, kann dies die gesamte Organisation beeinträchtigen und das Aufdecken von Ineffizienzen erschweren.
Efficio hatte kürzlich mit einem Unternehmen zu tun, bei dem mehrere externe Parteien jeweils verschiedene Teile des Liefernetzwerks bearbeiteten. Damit hatte die Supply-Chain-Abteilung keine Gesamtübersicht über die Kosten der Supply Chain und konnte Probleme oder auch Potenziale zur Kostensenkung nicht erkennen. Im Endeffekt betrieb sie eine fragmentierte Supply Chain. Manchmal finden sich die Informationen zu Kosten in unterschiedlichen, oft extern betriebenen IT-Systemen, zum Beispiel in ERP-, Lagerverwaltungs- und Transport-Management-Systemen. Dies erschwert den Zugriff auf präzise Kosteninformationen.
Es ist wichtig, dass Unternehmen einen klaren Überblick über die Kosten an den verschiedenen Stellen in der Supply Chain behalten. Die Daten sollten anhand einer einheitlichen Taxonomie konsolidiert werden. So können die einzelnen Posten für jeden Part der Supply Chain bis ins Detail nachvollzogen werden. Supply-Chain-Führungskräfte sind dadurch in der Lage, festzustellen, welche Teile weniger effizient als möglich arbeiten.
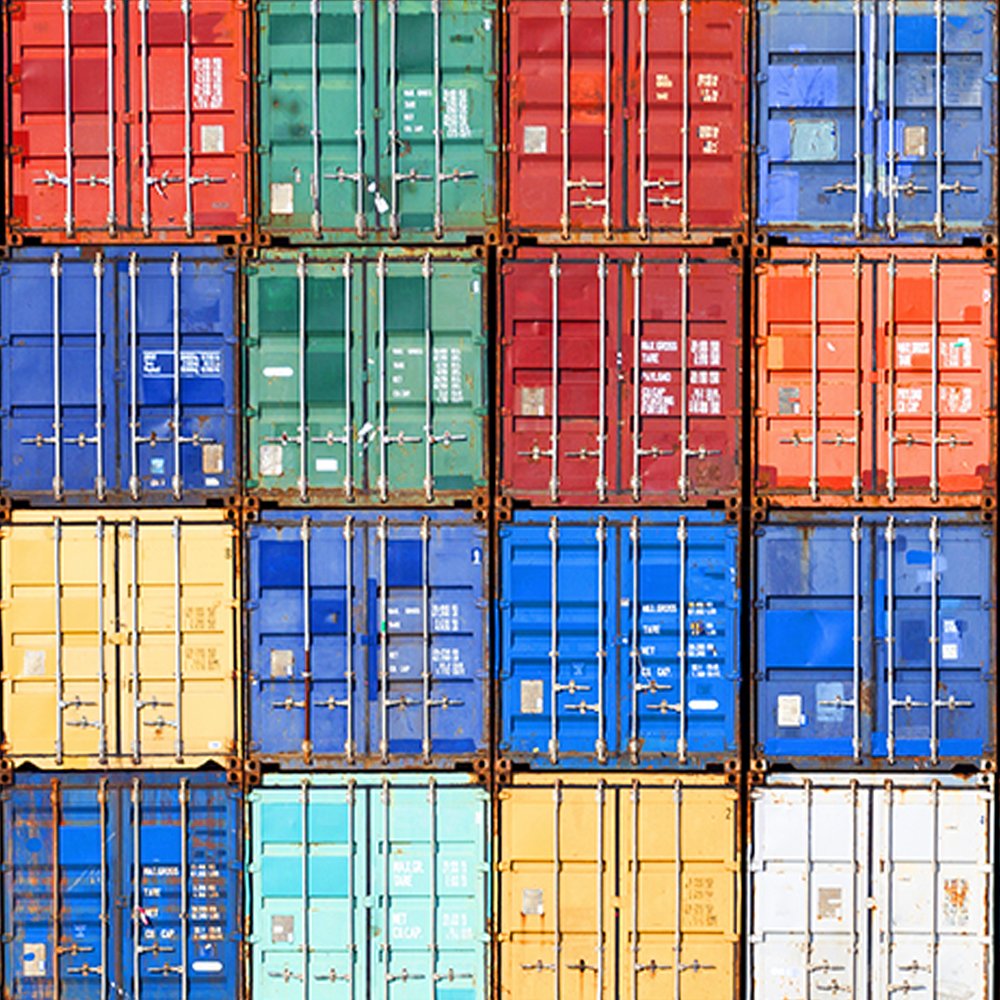
Fallstrick 6: Nicht auf Kunden hören
Eine todsichere Methode, um praktisch jedes Unternehmen zum Scheitern zu bringen, ist es, die Kunden nicht in den Mittelpunkt zu stellen. Dennoch orientieren sich Supply Chains oft mehr an den Anforderungen des Unternehmens – und hier speziell an jenen der Führungsebene – als an den eigentlichen Endkunden. Dies ist ineffizient und kann zu zusätzlichen, überflüssigen Kosten führen, da die Supply Chain nicht auf die Bedürfnisse der Kunden ausgerichtet ist.
Ein Beispiel hierfür wäre die fälschliche Annahme, dass die Kunden unbedingt eine Lieferung am nächsten Tag benötigen (möglicherweise inkl. Luftfracht, was erhebliche Logistikkosten erzeugen kann) – und das, obwohl die meisten Kunden eigentlich mit einer Lieferung innerhalb von drei oder sogar fünf Tagen zufrieden wären (und somit ein normaler Transport auf der Straße oder Schiene möglich ist). Solche Szenarien führen zu höheren Kosten, verbessern aber nicht die Kundenzufriedenheit, während andere – weit weniger kostenaufwendige – Maßnahmen sich deutlich stärker auswirken könnten.
In diesem Zusammenhang ist es wichtig, daran zu denken, dass die Kundenzufriedenheit einen direkten Einfluss auf das EBITDA eines Unternehmens haben kann. Es lohnt sich deshalb, darauf zu achten, was für die Kunden wirklich wichtig ist. Dies kann je nach Branche und sogar je nach Land unterschiedlich sein. Im Allgemeinen zählen zu den Faktoren, die tendenziell zu einer höheren Kundenzufriedenheit führen, eine konstant hohe Lieferleistung, wenige Fehler, eine größere Reaktionsfähigkeit innerhalb der Lieferkette und ein Premiumangebot.
Zeit investieren, um Zeit zu gewinnen
Jeder, der sich in einer Führungsposition innerhalb einer Supply-Chain-Organisation befindet, sollte sich regelmäßig fragen, ob seine Supply Chain Strategie noch zweckmäßig ist und weiterhin die Anforderungen erfüllt, die seine Kunden an sie stellen. Dies ist eine gute Gelegenheit, Bilanz zu ziehen und die aktuelle Situation zu bewerten. Gleichzeitig kann man erkennen, worauf man in einem Zeitraum von zum Beispiel zwei oder fünf Jahren hinarbeiten muss.
Jeder, der sich in einer Führungsposition innerhalb einer Supply-Chain-Organisation befindet, sollte sich regelmäßig fragen, ob seine Supply Chain Strategie noch zweckmäßig ist und weiterhin die Anforderungen erfüllt, die seine Kunden an sie stellen.
Dazu gehört auch, eng mit anderen Abteilungen zusammenzuarbeiten. So wird gewährleistet, dass die mit der Supply Chain betrauten Mitarbeiter die generellen Anforderungen des Unternehmens kennen und auch verstehen, wie sich diese in den nächsten Jahren ändern könnten.
Man muss zudem immer im Hinterkopf behalten, dass die Supply Chain letztlich dazu da ist, dem gesamten Unternehmen zu dienen, indem sie Waren durch eine Produktionsumgebung bringt, Produkte an Geschäfte liefert und die Verbindung zu den Kunden darstellt. Gleichzeitig verändert sich die moderne Supply Chain weg von einer linearen Ausrichtung hin zu einer zyklischen. Dabei gewinnen die Wiederverwendung und das Recycling von Komponenten und Teilen immer mehr an Bedeutung. Führungskräfte können dazu beitragen, dass die Supply Chain sowohl heute als auch zukünftig bestmöglich aufgestellt ist, indem sie jetzt für maximale Effizienz sorgen.