- Title
-
Six pitfalls to avoid when developing your supply chain
- Section
- Insight
- Summary
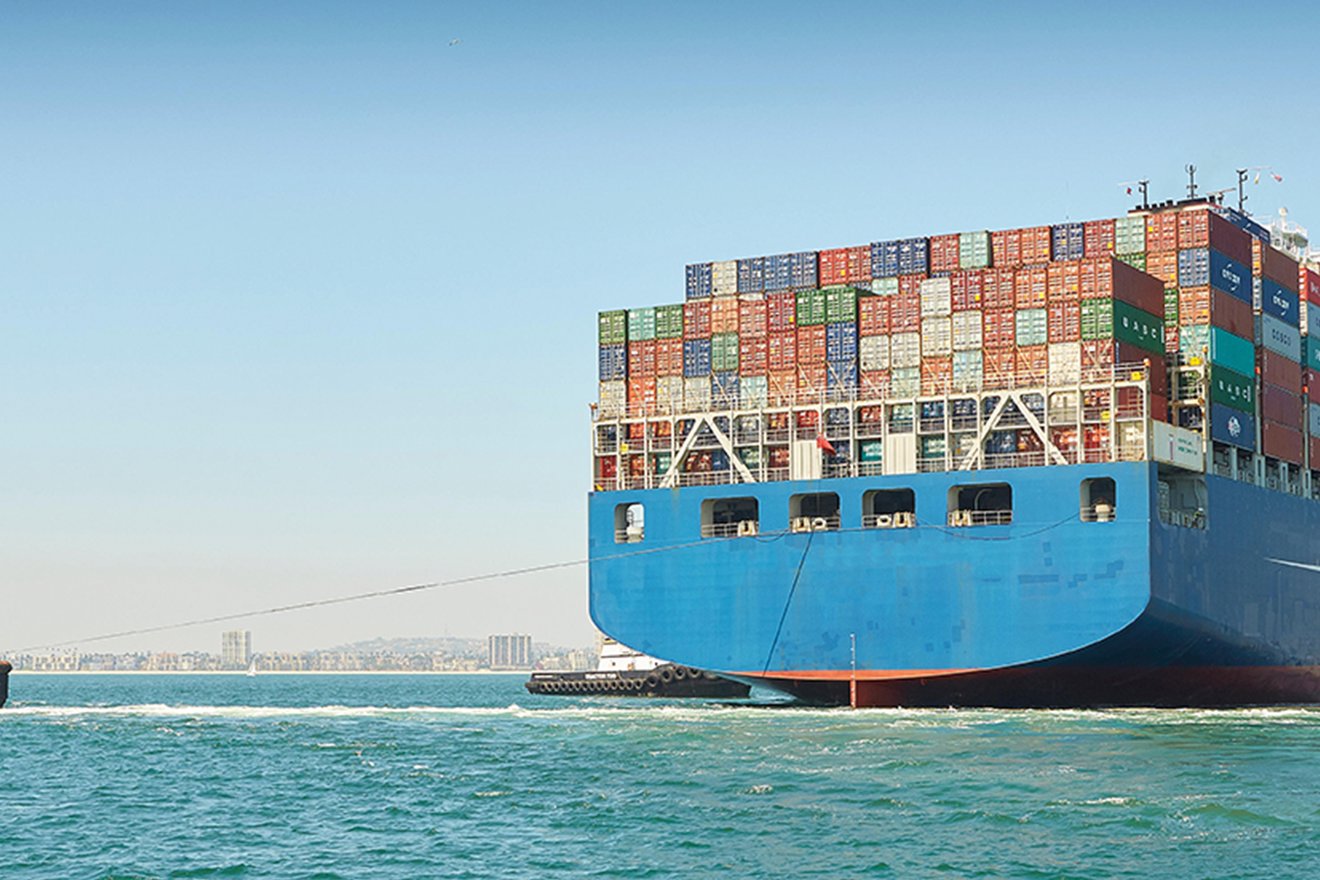
Most organizations develop their supply chain strategy in a piecemeal fashion over time, which means it can reach a point where it is no longer fit for purpose. We identify some common failings.
Every supply chain leader will understand the importance of having an efficient and well-managed supply chain that ensures products are delivered in the right quantities, on time, and as cost efficiently as possible. The strategy should align with the needs of the business and its customers. It should also minimize risk and ensure the organization operates in an ethically responsible and sustainable fashion.
Yet while most supply chain leaders understand the need for a comprehensive supply chain strategy, encompassing everything from planning to warehousing and delivery to stores or customers and returns, many businesses still operate inefficient supply chains.
There are a number of common pitfalls associated with supply chain strategy, but the good news is that tackling these means businesses can start to make significant improvements to their operations almost immediately, enabling you to plan ahead, reduce risk and significantly improve customer satisfaction at a lower cost.
…businesses can start to make significant improvements to their operations almost immediately, enabling you to plan ahead, reduce risk and significantly improve customer satisfaction at a lower cost.
Pitfall 1: Not having a strategy
One of the key factors a business should address is an inadequate or non-existent supply chain strategy. This tends to be common among businesses that have started small and where any approach towards managing the supply chain has been piecemeal. In such situations it’s often the case that the strategy was developed over time in a way that suited the company’s needs back then – perhaps focusing on a particular area such as logistics, warehousing or planning – but at no point since then has anyone sought to rationalize the supply chain or create a formal supply chain strategy.
This can result in a supply chain that is configured to deliver something that customers don’t value or the business attempting to solve a problem that doesn’t really exist. Any strategy that does exist is usually based on what the business required a decade ago, rather than what it needs today or in the future.
The supply chain strategy is the overarching principle that brings everything together and enables a company to extract the most value from its supply chain, so it’s vital that it’s considered. The starting point is to create a set of design principles to govern the supply chain and ensure this is documented and reviewed on a regular basis. Simply doing this will provide a firm foundation for future success.
Pitfall 2: Not having a fit-for-purpose operating model
An ill-thought-out operating model is another major pitfall. Many businesses will have a disparate set of operating models that are not connected to one another, having evolved over time in response to individual situations. Unless there’s a burning desire within the organization, businesses will rarely take the time to conduct a full evaluation of whether their supply chain is continuing to meet the challenges and requirements being placed on it.
The starting point is to conduct a full health check of the existing operating model(s) across a number of elements including strategy, processes and policies, performance management, technology and data, people, sustainability and cost. This can be carried out at a global level and for the individual components of the supply chain, such as planning, inventory, logistics and distribution, and warehousing.
It will ensure the strategy, processes and policies, and performance management systems, which govern the overall supply chain globally, are also implemented at a local level, underpinned by the right technology and people with the right skillset to support it. This should also be extended to incorporate sustainability, ensuring that all elements of the supply chain operate in line with the broader company goals and objectives in a cost-efficient manner.
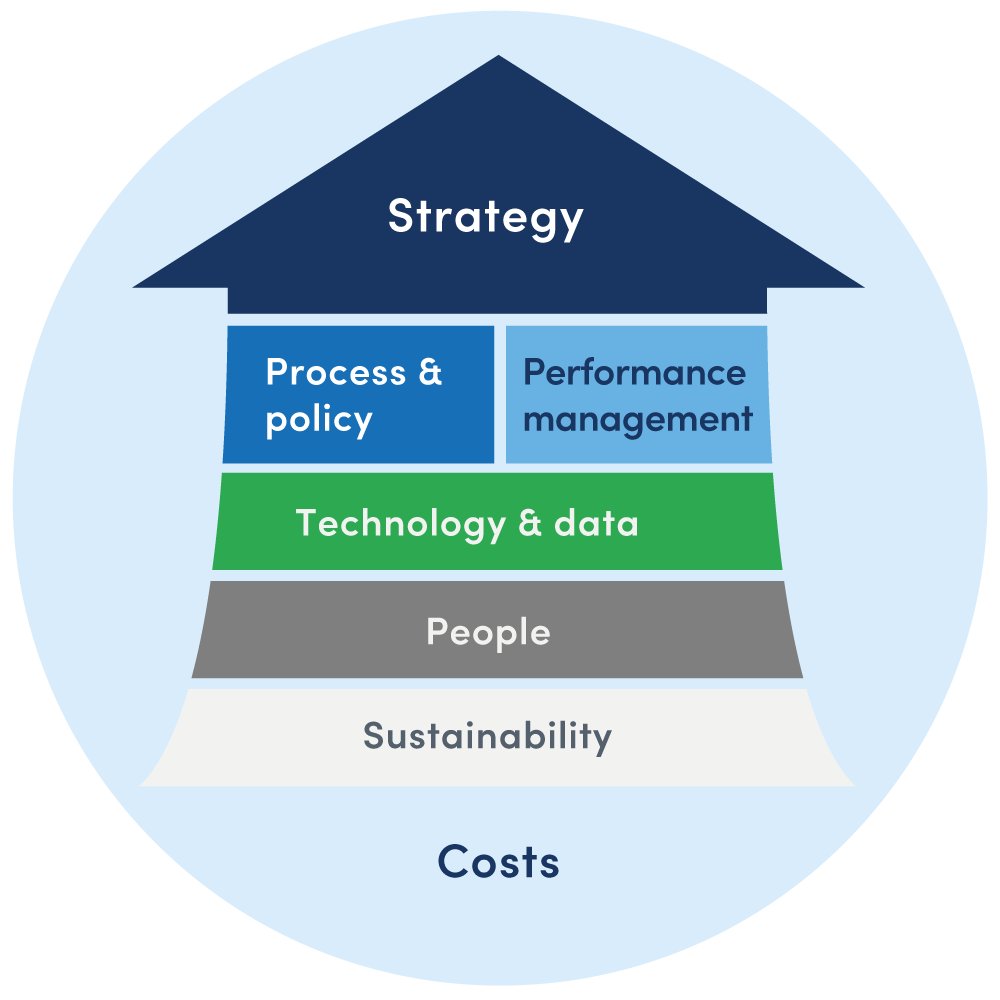
Fig 1: Efficio supply chain target operating model
Pitfall 3: Not aligning KPIs
Regardless of sectors, businesses have reached saturation point when it comes to supply chain key performance indicators (KPIs), to the point where many cannot even be regarded as ‘key’.
A number of KPIs being measured are reactive, often created in response to a particular issue and rarely set up organically. This can result in supply chain performance being pulled in different directions, with stakeholders and functions having separate – and sometimes conflicting – priorities. While local optimization is not uncommon, less prevalent is non-alignment at a global level. A business may locally optimize its own KPIs but, overall, they may not be aligned to broader business goals.
While local optimization is not uncommon, less prevalent is non-alignment at a global level. A business may locally optimize its own KPIs but, overall, they may not be aligned to the broader business goals.
An example here would be a logistics team that is consolidating shipments and achieving reduced logistics costs and high-trailer utilization as a result. However, the warehousing team would be inundated with volume on certain days of the week and would hire additional people to meet their KPIs around the receipt of incoming material.
In this case, both the logistics and the warehouse teams are meeting their local KPIs of high-trailer utilization and low-receipt time for incoming deliveries, but the overall cost to the network is not optimal.
The best solution in this scenario would be for the logistics team to work with the warehouse team and devise a delivery schedule, which may involve smaller shipments spread throughout the week. This could also help reduce the overall inventory levels.
Instead of taking an ad hoc approach to KPIs, resulting in too many metrics that do not fully align with broader business goals, businesses should implement a properly tiered KPI pyramid, where the highest KPIs are the executive metrics.
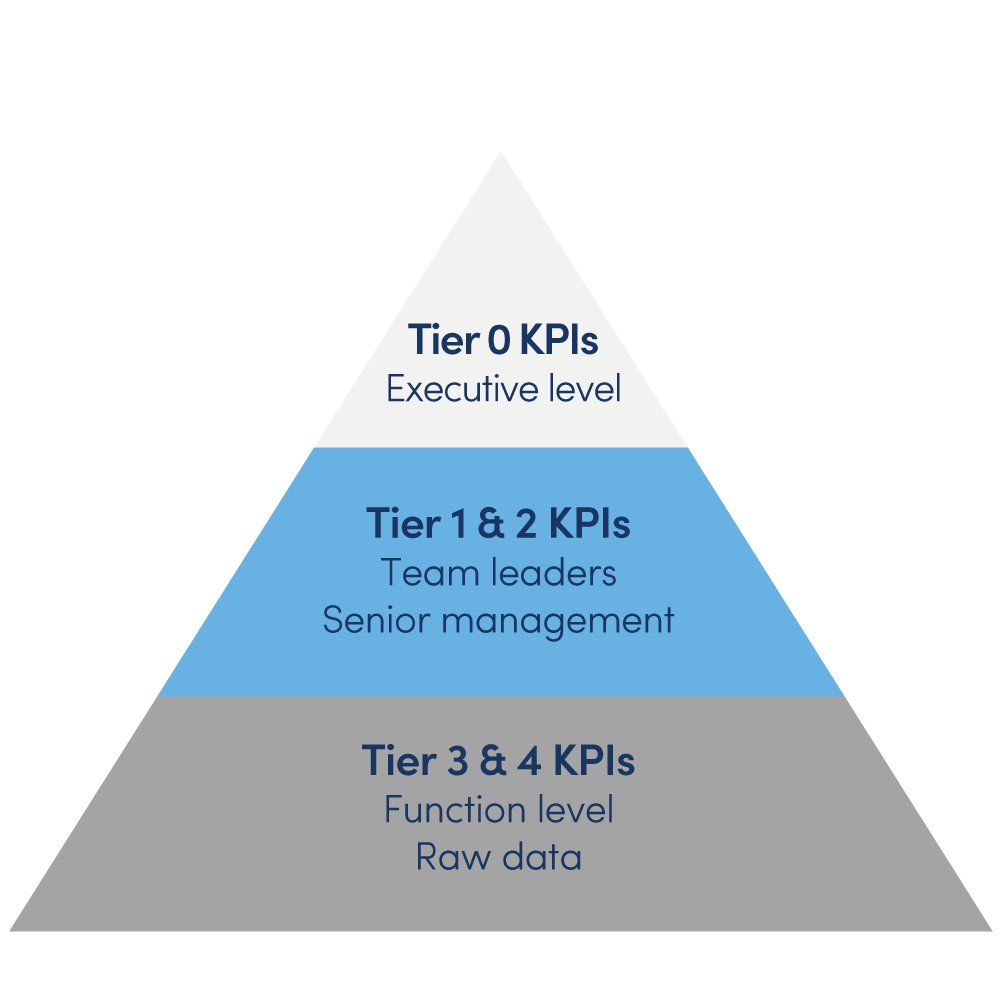
Fig 2: Tiered KPI pyramid
A manufacturing facility, for instance, may have top-tier KPIs based on manufacturing a certain number of engines per month or per year, with a set of subsidiary metrics that then dive into that KPI, potentially by function. This could be logistics delivered on time and in full or having 100% availability of machines and resources. This provides leaders with far greater visibility over any potential issues they may have, offering them the ability to drill down into specifics for any KPIs where the business may be underperforming.
A performance management framework should be deployed to assess, determine and implement relevant metrics at each level of the organization, and these should also tie into the metrics at the level above and below.
Pitfall 4: Not conducting a supply chain resilience assessment
Failing to conduct a supply chain resilience assessment is another common pitfall. There are several factors – both internal and external – that could impact on the ability of a supply chain to function effectively, or that could create negative publicity for the business.
Brexit is a major concern for many UK and global businesses currently, requiring organizations to think about how they would keep manufacturing facilities running or shelves stocked in retail outlets. Other potential threats could include supplier failure, disruption to travel routes (for example, the Icelandic volcano eruption) or increasing raw material costs, while reputational risks could stem from child labor, poor environmental or health and safety practices, or even modern slavery being discovered anywhere in the extended supply chain.
At Efficio, we have identified 14 categories of risk against which businesses should test their resilience and which they should use to develop contingency plans to mitigate the potential danger posed.
Pitfall 5: Not considering the network cost
Failing to understand the cost of each element of the supply chain can also hamper the organization by making it difficult to determine which aspects are not working efficiently.
Efficio recently came across a company that had multiple external parties, each handling different parts of its network. This meant the supply chain function didn’t have overall visibility over what the supply chain cost, meaning they were unable to identify any issues or opportunities for cost reduction and were operating a fragmented supply chain. Sometimes, costs are stored in disparate IT systems – often hosted externally – such as ERP, WMS and TMS packages, which makes it difficult to access accurate information on costs.
It is vital that businesses have a clear line of sight over the costs at various points in the supply chain. Data should be consolidated and a uniform taxonomy created so that the cost elements can be drilled down to a detailed level for each element of the supply chain. This will enable supply chain professionals to identify which parts are not operating as efficiently as they could be.
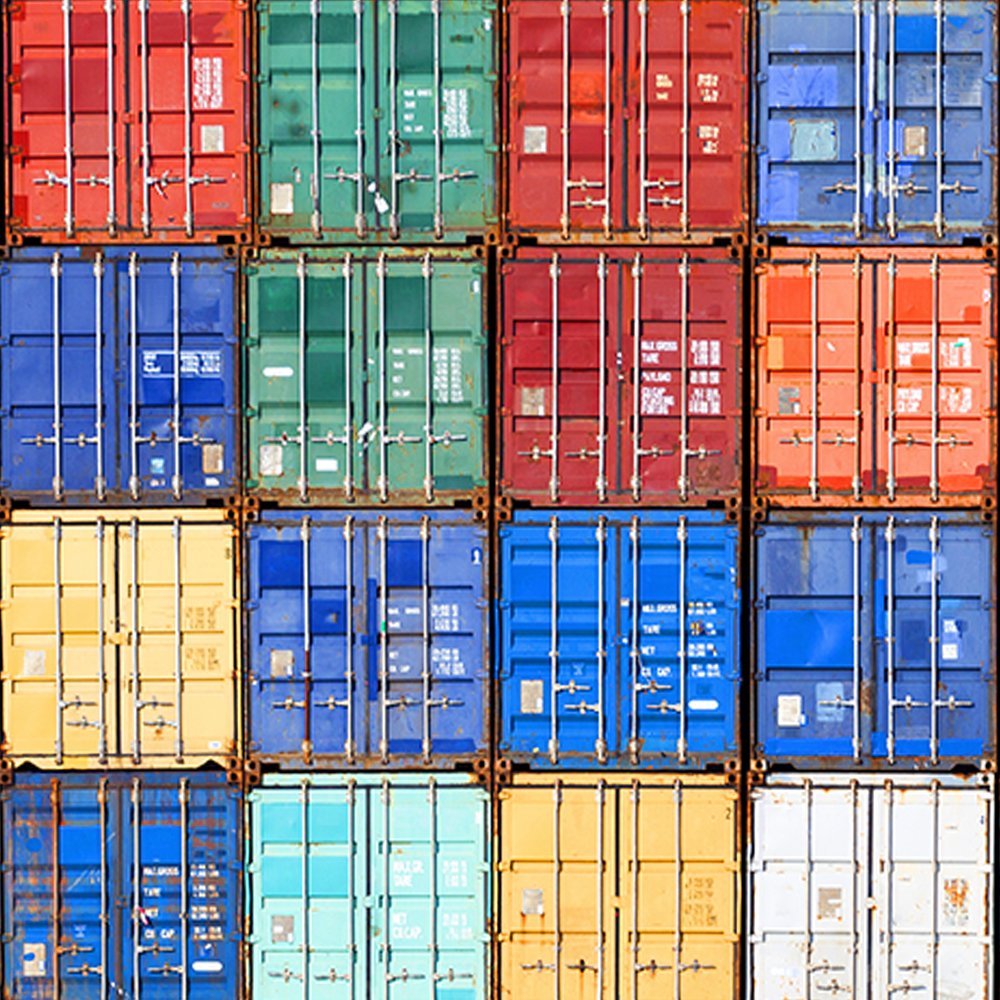
Pitfall 6: Not listening to customers
Not making the customer the focus of the business is a recipe for failure for any company. Yet supply chains are often built around the requirements of the business – in particular the senior leadership team – rather than end-customers. This can create inefficiencies and unnecessary costs, and means the supply chain is not optimized in line with customer requirements.
An example would be a mistaken belief that customers require next-day delivery (which can create significant logistics costs, potentially requiring shipment by air) when most customers would have been happy with a three or even five-day window, with items transported by road or rail. Situations such as these result in higher costs but do not improve customer satisfaction, whereas other less costly initiatives could have the opposite effect.
It is important to remember that customer satisfaction can have a direct impact on an organization’s EBITDA, so it’s worth paying attention to what really matters to customers. This will differ by industry and even country, but common factors that tend to result in higher levels of customer satisfaction include a consistently high delivery performance, a reduction in errors, greater supply chain responsiveness and developing a premium offering.
Take time to make time
Anyone in a leadership position within a supply chain organization should ask themselves periodically whether their supply chain strategy remains fit for purpose and continues to meet the requirements that their customers are placing on it. This is a good opportunity to take stock and assess the current situation and identify where it needs to be in two or five years’ time, and start working towards that. This also means working closely with other departmental functions, ensuring those in the supply chain function fully understand the wider needs of the business and how these may change over the next few years.
Anyone in a leadership position within a supply chain organization should ask themselves periodically whether their supply chain strategy remains fit for purpose and continues to meet the requirements that their customers are placing on it.
It’s important to remember too that the supply chain function is ultimately there to serve the broader business, by bringing goods through a manufacturing environment, delivering products to stores and connecting with customers. At the same time, the modern supply chain is moving from being linear to cyclical, where reusing and recycling components and parts is becoming more prevalent. By taking steps now to make sure the supply chain is operating as efficiently as possible, leaders can help ensure it remains fit for purpose, both now and in the years to come.