- Title
-
COVID-19: Key short-term actions for manufacturers to take
- Section
- Insight
- Summary
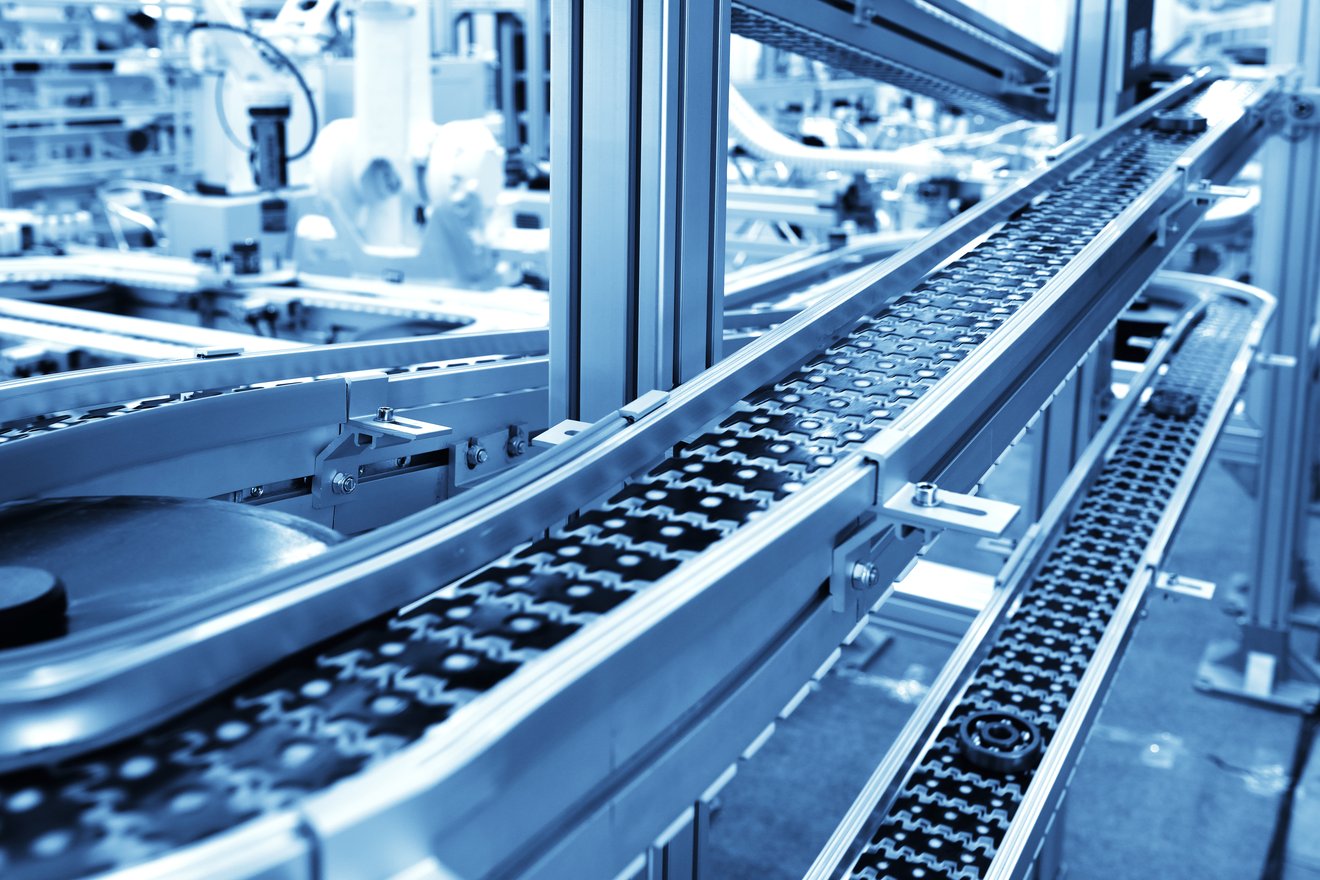
As COVID-19 impacts manufacturing supply chains, which key short-term actions should be taken?
From reduced workforces to complete shutdowns, many industries and sectors are suffering at the hands of the COVID-19 outbreak, and manufacturing is taking one of the largest hits.
Supply chains and associated lead times are fluctuating wildly, impacting business sales around the world as production is delayed. To stay afloat, businesses should ask themselves the following key questions:
- What are the key risks posed by the crisis?
- What actions can be taken in the short term?
- Are there any benefits that can be achieved?
- What will we do when the pandemic is over?
Assess, forecast, identify and measure
Firstly, businesses should develop detailed risk management programmes. Assess the business continuity and the financial stability of your company, and forecast the possible future loss of sales. Identifying high impact areas, critical suppliers and measuring workforce safety also play a key role to formulate a more effective response.
Depending on general lead times, products manufactured in Q2 of this year may still affect sales in Q3 and Q4. This provides insight for businesses on annual revenue impact, as well as which product lines and associated spend categories might be affected most – especially if demand seasonality exists.
What actions can I take to minimise the impact on revenue?
Several actions can be taken in the short term. The most common practices for business continuity include sourcing products and services from alternative countries and negotiating supply security with incumbent vendors through back-up production facilities.
To cope with delayed manufacturing, air freight for distribution is likely to increase, as it replaces ocean and ground transit. Passenger aircrafts are already being utilised purely for the transportation of goods. Manufacturing business must weigh the costs of increased freight versus the potential loss of sales in order to pinpoint what the optimal option would be.
One might even decide to halt certain production lines as opposed to incurring more delays. Businesses may want to monitor and evaluate where in the lifecycle it makes sense to pull out, as opposed to waiting too long and subsequently seeing the business fail to convert sufficient sales.
Are there any benefits that can be achieved?
Beyond minimising impact, businesses can also act quickly during this time to achieve high-performing outcomes, such as greater profit. For example, as there is less product availability during the crisis, wholesalers may decide to refocus their distribution, favoring high-performing outlets at the expense of lower performing ones. In turn, while overall sales may fall, there may be significant opportunity to increase profit margins. Improved procurement through cash release, renegotiation of commitments, tactical sourcing, adjustment of production planning, enhanced stock levels and demand optimisation can all rapidly support bottom-line improvement.
What will we do after the pandemic recovers?
How should we best prepare for after the situation recovers? As demand for goods decreases, supply will adjust. When supplies are short, the most important question for a manufacturing business becomes, how do I become a priority to my suppliers? You may need to pay more to your suppliers, especially if you are not a critical client. However, some suppliers might be more interested in serving customers with whom they have good relationships, as opposed to simply increasing charges. In this instance, you have the option to seek alternative vendors, or negotiate with incumbent suppliers, perhaps offering longer term commitment where possible. These are compromises which may be more valuable in the long run for both parties as they build on that partnership in difficult times.
Once this pandemic is contained, demand will peak again. Manufacturing firms will need to ramp up production and customer service, as we are currently witnessing in several Chinese provinces. The best teams will know what to anticipate in terms of demand increase and how to respond accordingly. These teams also know that they need to act quickly to secure their volume in the supply chain and tap into their strong supplier relationships.
Moving forward
In the face of uncertainty, there are several elements that manufacturing firms can control in order to minimise the impact of COVID-19 on their supply chains. When firms better understand the potential risks induced by the virus, they can decide where focus might be more critical. Reduction in demand, alternative modes of transport, digitalisation, strategic sourcing, a cash release programme and product- line focus are all possible actions that can influence the bottom line. The key will be to work fast and prepare, starting right now.