- Title
-
Onshore manufacturing: more than a trend
- Section
- Insight
- Summary
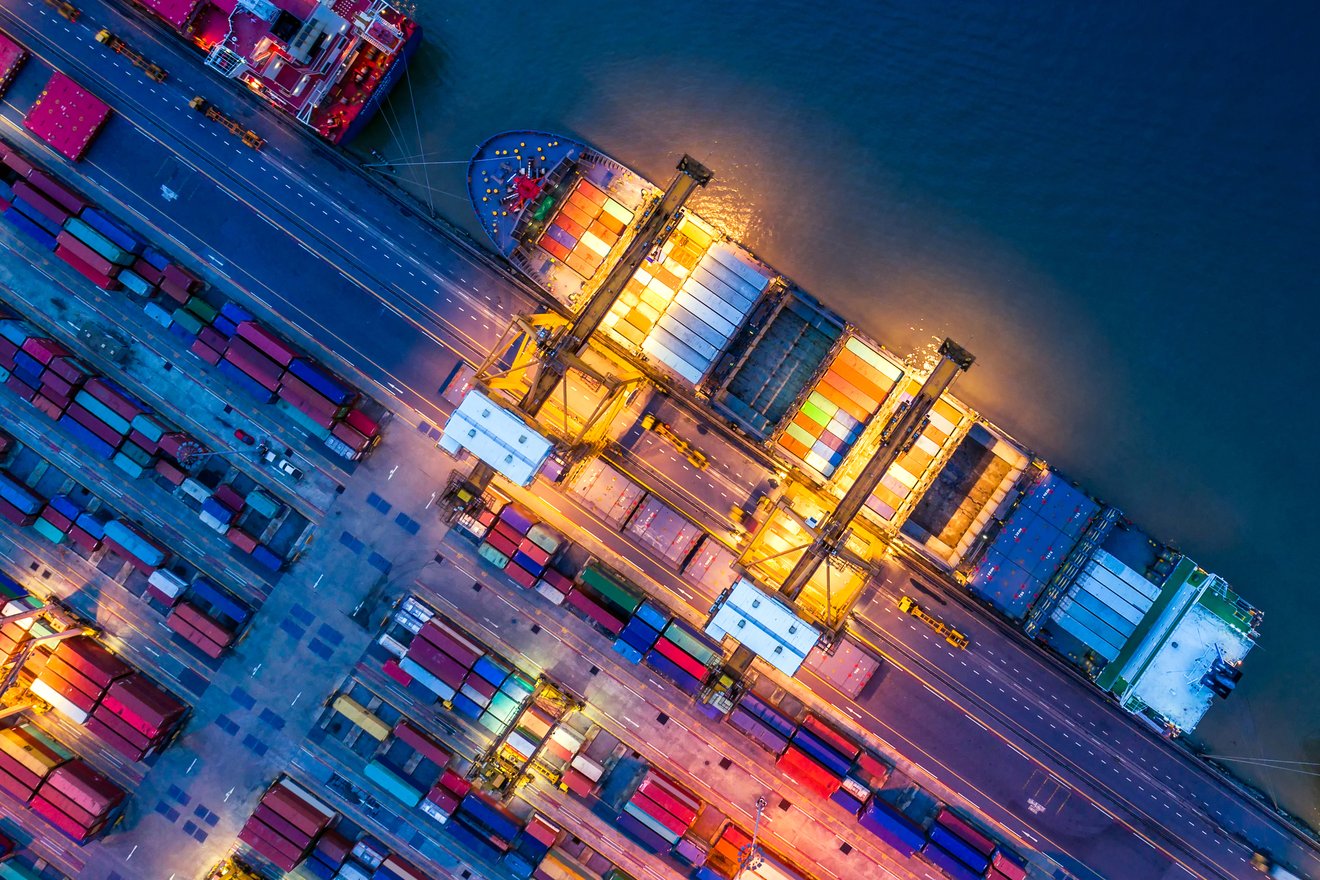
Rising overseas labour costs and Brexit are just two reasons why we believe the recent increase in onshoring of manufacturing operations is here to stay. Is your supply chain management equipped for changing times?
Since the 1970s, there has been an inexorable trend towards offshoring the manufacture of components and physical goods to low-cost countries. It helped make the Chinese economy the second largest in the world, and fuelled the rise of other economies as diverse as Singapore and Mexico.
In recent years, however, this activity has slowed. Organisations have taken steps to nearshore or onshore manufacturing, either bringing operations back to the UK or closer to home in markets such as Eastern Europe.
Changing economics
There are a number of reasons for this, the most prominent being changing economics.
Since 2000, labour costs in China have risen by around 10% every year. This means that today, the wage differential with the UK is often as little as 10-12% when productivity and the strengthening yuan are factored in.
When shipping and storage costs are brought into the mix, the benefits of basing activity in China are no longer as great as they once were – not to mention practical issues such as language, cultural barriers and time zone differences.
Having an extended supply chain also brings its own risks (see our article Procurement risk & where to find it). Due to the number of journeys and nodes, supply chain disruption is increasingly likely.
In 2011, the floods in Thailand and the Fukushima Daiichi nuclear disaster in Japan made businesses realise how vulnerable they were to events beyond their control, with many re-evaluating where they should base their operations.
More recently, sabre-rattling between US President Donald Trump and the North Korean leadership fuelled deep fears of military action, putting South Korean companies and their supply chains at considerable commercial risk.
Other issues such as modern slavery, child labour, and bribery and corruption have deterred businesses from looking at locations in other low-cost economies as an alternative to China.
Brexit effect
Brexit is also impacting UK businesses, causing uncertainty over customs, tariffs and border controls.
Had the UK voted to remain in the EU, it’s likely more businesses would have looked to nearshore their operations. Markets such as Poland, Hungary and Romania still offer an attractive wage differential, but the risks and transport costs are lower.
However, as it is, UK organisations are now beginning to take a harder look at onshore manufacturing. This includes businesses that have already brought manufacturing back from China and based it in lower-cost European countries.
A survey by the Chartered Institute of Purchasing and Supply (CIPS) in November 2017 found that 40% of UK businesses are looking to replace their EU suppliers. Meanwhile, the recent boom in UK manufacturing – HIS Markit’s Purchasing Managers’ Index hit a four-year high in December – may be partly due to a desire to make goods in the UK.
A survey by the Chartered Institute of Purchasing and Supply (CIPS) in November 2017 found that 40% of UK businesses are looking to replace their EU suppliers.
Challenging times
Yet bringing manufacturing back to the UK will have its own challenges. For example, around 50-60% of the gross value-added material in the automotive sector is sourced from Europe. Untangling these contracts and operations will be a complicated process. Plus, many sectors will face limited capacity in the UK, in terms of both numbers of suppliers and the volumes they can handle.
Then there’s the post-Brexit trade environment. One of our clients imports ethanol from the EU, before exporting waste product back to the original manufacturer. Once we leave the EU, such activities may be subject to tariffs, border checks and even trade restrictions.
However, running a tender exercise showed us that the UK market is limited in its ability to deal with this scenario.
We therefore explored the possibility of having our client invest in a UK supplier, to increase its capacity and build a waste stream facility of its own.
Stories such as this are likely to become common in the future, as manufacturers discover that onshoring requires patience to find credible suppliers and, often, a willingness to jointly invest in new capacity.
There’s also a danger that businesses relax the scrutiny paid to potential supply chain disruption once sourcing is back onshore. Though the suppliers may be trusted and lead times shorter, supply chains will still require ongoing monitoring.
Future planning
Bringing back manufacturing from low-cost economies, coupled with a reaction to Brexit, means fundamental change for many UK manufacturers and their suppliers. It’s vital that businesses consider both their broader strategy and practical response to changing economic realities.
Bringing back manufacturing from low-cost economies, coupled with a reaction to Brexit, means fundamental change for many UK manufacturers and their suppliers.
The questions supply chain and procurement managers should be asking themselves are: “Do I understand how my supply chain costs will change over the next five years? And am I positioned to make more use of local suppliers where it is sensible to do so?”
Only then can they position themselves not just to survive, but to thrive in the years ahead.