- Title
-
COVID-19: What the ‘new normal’ means for CPOs?
- Section
- Blog
- Summary
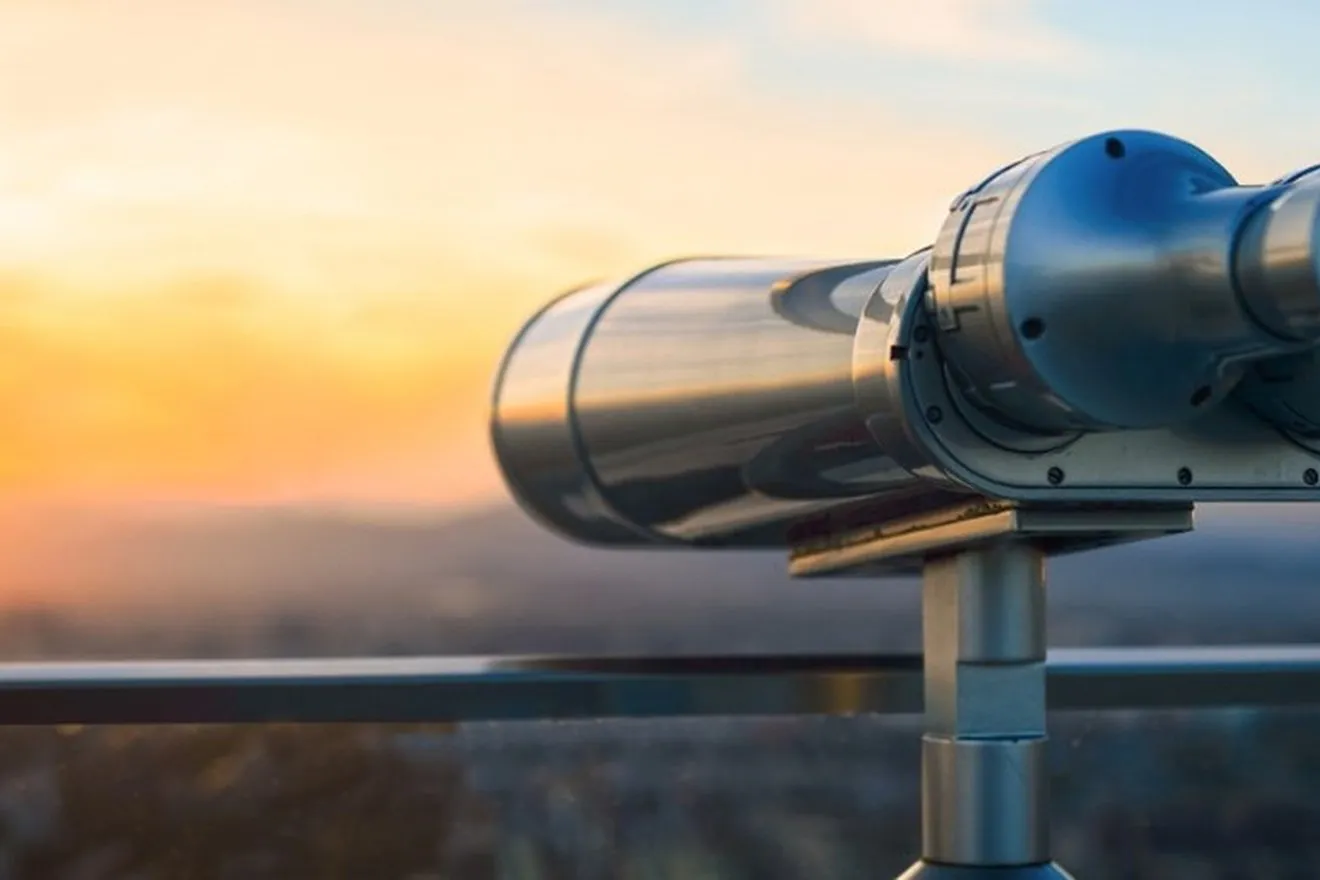
This blog post was published 12 May 2020, based on information available at that time.
The primary focus for CPOs over the last few months has markedly shifted to responding to the immediate COVID-19 crisis managing disruptions. As countries start to de-escalate, CPOs should now fully embrace supply chain resilience.
Mark Schneider, chief executive of Nestlé, recently urged procurement staff to be prepared for the next phases of the crisis, “Please get ready for the storm to hit – because hit, it will. We need to focus our efforts on securing supplies, manufacturing and logistics every step of the way. For those areas that are not affected yet, get prepared by building inventories of critical supplies and products.”
In many countries, people are getting back to work on site. There will still be local outbreaks of COVID-19, which will continue to disrupt supply chains; however, these will become more and more rare. But what lasting effects will all of this have on the CPO's agenda?
Adapting to the new normal
The lean mindset has been prevalent in most procurement functions for some time. Removing duplicate suppliers, sourcing from lower cost countries, standardising parts to create volume leverage and reducing inventories have created the cost savings that boards and investors wanted to see. This has created significant efficiencies, and global sourcing has delivered high quality products at a lower cost. Asian supply chains, for instance, have been resilient even after crises such as the 2004 tsunami in southeast Asia.
The new normal is one in which production can simply halt in parts of the world. China's production went almost to a standstill in February; European and US production did the same in April.
This has been particularly challenging for manufacturing clients who, for instance, had a single source of supplies for critical parts and limited strategic inventory to cover a real risk to their supply chain. Most CPOs are conscious of this but, until recently, building resiliency in the supply chain brought additional cost that could not be justified. For certain categories and critical supply chain components, now is past time to re-assess this issue.
The challenge for CPOs is now to drive their organisations’ efforts to model, quantify the cost of the resilience and prioritise where to invest.
The ‘stress test’ areas will include:
- Supply transparency: Have we lost transparency through the tiers of our supply chain? Do we have a geographical bottleneck in our upstream supply chain?
- Supplier redundancy: Have we pushed single sourcing too far?Should we consider supplier doubling for critical components?
- Insource/outsource balance: How will social distancing reduce our manufacturing output, and what outsourcing capabilities do we need to line up to meet the demand? On the other hand, should we look to re-insource critical/vulnerable elements of the supply chain?
Every supply category will have a different risk profile and strategy post COVID-19. There cannot be a blanket approach to this crisis. Creating additional stock on non-critical components would be even more of a mistake when companies are short of cash.
This new modelling will need to assess on a case-by-case basis how much more companies are ready to pay for goods or services that increase their supply chain resilience. It could be 2% for marketing services and 20% for PPE, for instance. Procurement savings could be partly reinvested in a ‘supply chain resilience’ reporting line that would be become part of the sales and operating planning process.
Prepare now
Overall, this approach will elevate the discussions between the CPO, CFO and CEO and make supply chain resilience a regular top item on the board agenda.
There is no doubt that 2020 will leave a lasting impact on what is expected from procurement. CPOs should now source components from multiple locations and from multiple suppliers. They should be prepared to pay more for backup options and create larger inventories for critical parts. This will in turn create supply chains that may be slightly less cost efficient in the short term but far more robust for when the next crisis hits.