- Title
-
Trasformazione Supply Chain di un produttore ferroviario
- Section
- Case Study
- Summary
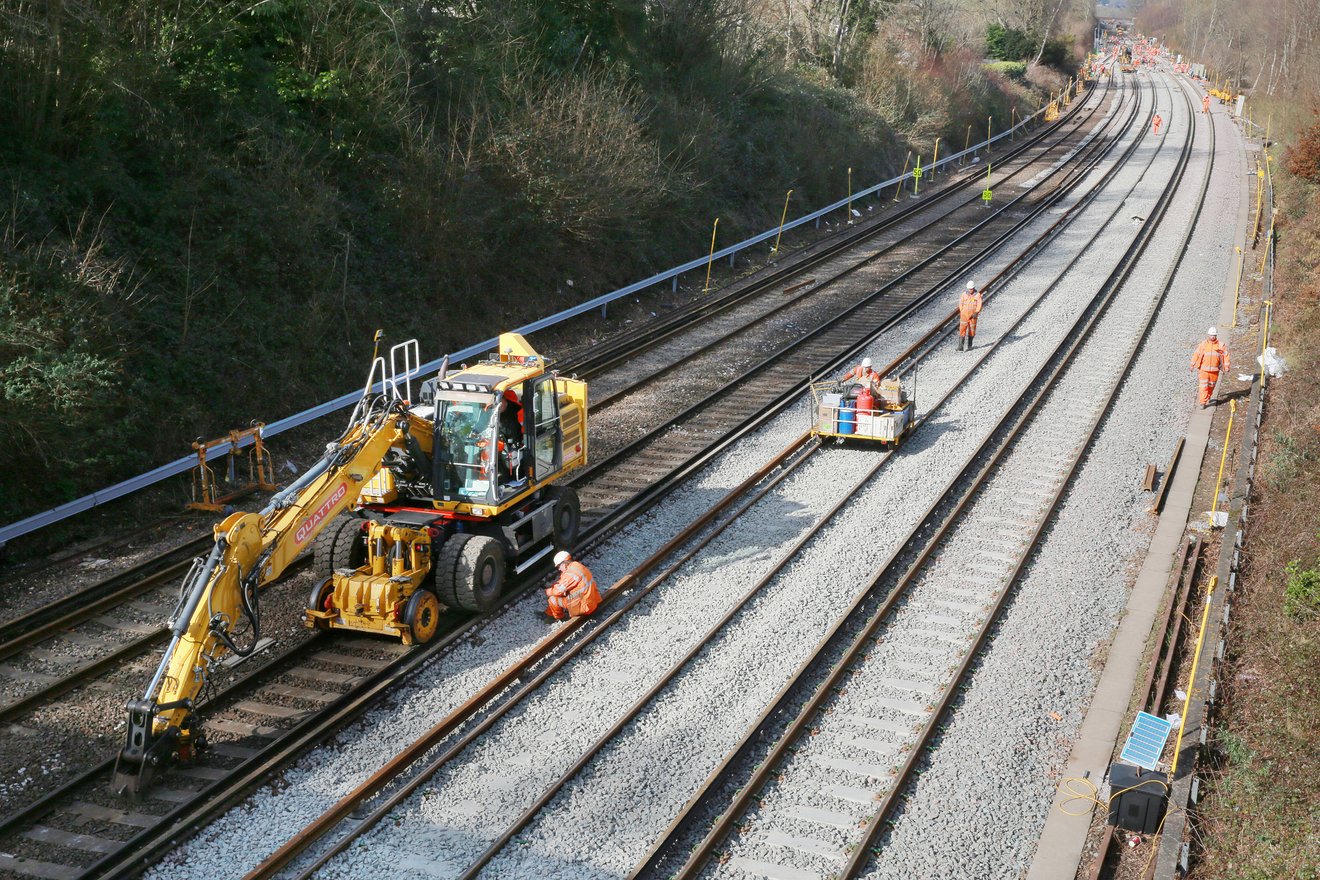
Un importante produttore di materiale rotabile ha recentemente aperto una nuova struttura produttiva nel nord dell’Inghilterra; si è trattato di un grande successo per il settore, per la regione e per il produttore stesso. Tuttavia, le gravi problematiche legate alla gestione dei materiali hanno causato ritardi sulla consegna dei nuovi treni e generato salate penali.
Con una disponibilità di materiali (la percentuale di materiale pronto all’uso lungo la linea di produzione su base quotidiana) ben al di sotto del target, la produzione era indietro rispetto al piano. Viste le imminenti scadenze, l’azienda ha ingaggiato Efficio con urgenza per identificare e risolvere il problema.
Efficio ha rapidamente identificato le cause di fondo e ha adottato una serie di misure volte a risolverle, generando risultati veloci e significativi. La disponibilità dei materiali è aumentata quasi del 50%, di conseguenza gli obiettivi dei clienti sono stati raggiunti e la produzione è rientrata sui binari giusti.
Contesto
Con l’apertura di un nuovo stabilimento per la produzione di treni nel nord dell’Inghilterra, il cliente avrebbe “riportato a casa la produzione ferroviaria”, creando anche 700 nuovi posti di lavoro. Inizialmente lo stabilimento si è concentrato sulla produzione della prima commessa importante del cliente, centrata sulla realizzazione di 173 treni.
I treni sarebbero stati progettati all’estero e costruiti in Inghilterra dalle esperte maestranze locali coadiuvate dal personale di svariati siti del cliente in tutto il mondo, coinvolto per assicurare il trasferimento delle conoscenze nelle fasi iniziali. Tuttavia la mancanza di una esperienza specifica sulla supply chain ha fatto sì che le parti necessarie non fossero sempre disponibili nel momento giusto lungo la linea, causando fermi e ritardi di produzione.
Alla luce delle salate penali previste in caso di ritardo, qualsiasi contrattempo poteva produrre conseguenze gravi. Efficio si è impegnata a risolvere con urgenza i problemi all’origine di tali ritardi.
È stato subito chiaro che uno dei problemi principali era la carenza di dati di qualità, che rendeva impossibile una buona gestione della supply chain. Le problematiche legate al gestionale dello stabilimento si traducevano in un sistema di pianificazione del fabbisogno dei materiali (MRP - Material Requirements Planning) poco efficace. Il problema era poi aggravato dai diversi stakeholders, ognuno dei quali aveva una propria idea sui processi relativi alla supply chain; in sostanza, arrivare alla radice dei ritardi era molto difficile.
Le altre problematiche includevano la duplicazione delle parti (la stessa parte veniva identificata con diversi codici) e la difficoltà del transito delle parti dai magazzini esterni a quelli interni dello stabilimento a causa delle difficoltà nel prevedere i fabbisogni futuri. Il personale del magazzino e di controllo dei materiali doveva passare ore a etichettare nuovamente e riconciliare diversi codici parte per evitare “false carenze” lungo la linea di produzione.
Il lavoro di Efficio ha permesso al cliente di comprendere con precisione la causa dei ritardi e i problemi da affrontare. Le misure introdotte hanno risolto efficacemente il problema della disponibilità dei materiali in un breve lasso di tempo e in un contesto di urgenza elevatissima.
Approccio
Efficio ha coinvolto specialisti di supply chain ed esperti di settore per avere una visuale completa dell’intera supply chain e identificare le problematiche che vi si annidavano. Dopodiché il processo ha previsto una serie di iniziative volte a risolvere tali problemi, tra cui:
- Affiancamento del personale del cliente attraverso l’assegnazione a collaboratori di Efficio di ruoli chiave lungo la linea di produzione (responsabile della supply chain e del controllo dei materiali) per dare impulso immediato alla conoscenza e alle competenze in materia di supply chain, oltre a un team di progetto di Efficio attivo sul campo.
- Creazione e applicazione di una serie di strumenti su misura per affrontare il problema dei dati, incluso un mini gestionale finalizzato a far corrispondere i fabbisogni di produzione alla disponibilità dei materiali, e calcolo della disponibilità per tutti i treni in produzione sull’arco di 12 mesi. In questo modo il team di controllo dei materiali per la prima volta è stato in grado di identificare e risolvere potenziali carenze prima che queste diventassero un problema. Sviluppo degli strumenti per affrontare il problema attraverso il trasferimento di materiali da magazzini esterni a magazzini interni
- Ottimizzazione delle giacenze creando e applicando un processo di acquisto dei materiali per categorie, spostando quasi il 40% del picking quotidiano in un sistema Kanban e liberando così notevoli risorse.
- Chiarimento di ruoli e responsabilità relativi al team per i master data dei materiali, generando notevoli miglioramenti nella gestione dei dati. Sviluppo di uno strumento su misura per gestire il problema della duplicazione dei codici parte.
- Sviluppo di una piramide di KPI in cui ogni livello è legato a quello superiore, per assicurarsi che tutte le funzioni perseguissero lo stesso obiettivo.
Risultati
Il lavoro di Efficio ha permesso al cliente di comprendere con precisione la causa dei ritardi e i problemi da affrontare. Inoltre, le misure introdotte hanno risolto efficacemente il problema della disponibilità dei materiali in un breve lasso di tempo e in un contesto di urgenza elevatissima.
La disponibilità dei materiali è aumentata quasi del 50%, dal 65% all’inizio del processo al 95%, permettendo di raggiungere gli obiettivi del cliente e contribuendo a mitigare gli enormi costi legati ai fermi di linea.
Oltre a garantire gli obiettivi principali, il coinvolgimento di Efficio ha offerto al cliente una serie di altri vantaggi.
Gli strumenti su misura sviluppati da Efficio hanno liberato una notevole quantità di tempo per gli addetti al controllo dei materiali e del magazzino, permettendo loro di concentrarsi su altre problematiche, ad esempio riducendo il tempo necessario a prevedere i fabbisogni futuri da 1,5 ore a meno di dieci minuti.
Gli strumenti e i processi di KPI introdotti da Efficio hanno fornito preziose informazioni gestionali precedentemente non disponibili. Queste informazioni hanno posto le basi per l’approccio di Efficio e continuano ad essere utilizzate dalla direzione dello stabilimento per identificare potenziali problemi e le relative soluzioni.